pH值 |
冲击次数 |
破裂现象 |
破裂片数 |
合格率/% |
4.0 |
5 |
层裂 |
20 |
0 |
5.0 |
8 |
层裂 |
20 |
0 |
6.0 |
10 |
层裂 |
20 |
0 |
8.0 |
20 |
碎裂 |
5 |
75 |
10.5 |
20 |
碎裂 |
3 |
85 |
13.0 |
20 |
碎裂 |
6 |
70 |
注:上述数据为[Ni2+]∶[H2PO2-]=0.5时测定。
从实验结果可以看出,化学镀镍层中的成分对PTC元件耐工频电流冲击性能的影响很大。事实上,这和化学镀镍后在PTC元件内产生的应力有关,化学镀镍电极的总应力是由热应力和内应力组成的,内应力来自沉积镀层和原子缺陷[3],改善合金结构可望得到消除,所以本文主要讨论热应力。
进行耐工频电流冲击时,PTC元件的瞬时功率可达到150W左右,在很短的时间内从室温升到居里温度以上,在此过程中伴随有晶相变化,同时由于元件两个表面的金属镍电极与元件之间的散热存在差异,使元件表面处和元件体内有较大温差,这一温差产生部分热应力。更重要的是,由于镀层与陶瓷体的热膨胀系数不同,而镀层与陶瓷基体的强制结合又阻止它们的自由伸缩,在镀层中便产生了热应力,由于PTC陶瓷足够厚,温度变化引起瓷体的弯曲可以忽略,热应力ST可以由下式精确计算〔4〕:
ST=(αN-αC).△t.EN (1)
式中:αN,αC分别为镀层和陶瓷基体的平均热胀系数,对Ni-P合金镀层而言,25~300℃范围内基本为一常数,约为13×10-6℃-1;而钛酸钡单晶在居里温度TC附近发生相变,由四方晶系转变为立方晶系,并伴随有晶胞体积变化。因而钛酸钡陶瓷的热膨胀系数α在TC处变化将是不连续的。Δt为沉积镍层时瓷体温度与工作时瓷体温度之差。EN为镍层的弹性模量。若计算出的ST为正,则镍层受张应力作用,此时PTC元件受电流冲击时表现为碎裂;ST为负,则镍层受压应力作用,此时PTC元件受电流冲击时表现为层裂,热应力类型如图1所示。热应力的类型和大小可通过合理选择Ni-P合金层及沉积温度来控制。
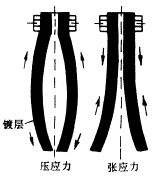
图1 热应力的类型示意
在PTC陶瓷上进行化学镀镍时,可供选择的沉积温度范围相对较小,所以只能通过选择Ni-P合金层组成即改变合金层中磷镍含量的比例来控制,而磷镍含量的比例与镀液中还原剂的浓度及镀液pH值有关,还原剂浓度与磷含量成正比,pH值与磷含量成反比。
根据实验结果,可以发现对磷含量高的元件,在进行工频电流冲击时,大多发生层裂。而磷含量低的元件,大多发生碎裂。作者认为,PTC元件在受电流冲击时,元件迅速升温,由于镀层及瓷体膨胀系数不同及开始时温度的差异,镀层与瓷体受热膨胀后伸长长度并不相同,简单地,伸长长度ΔL与膨胀系数α及温度变化的关系如下:
ΔL=αL0(t-t0) (2)
式中:t0为冲击前温度;t为冲击时瓷体与电极的温度。在冲击时,由于瓷体与电极的电阻率的差异,受电流冲击后的tC(瓷体)与te(电极)也不尽相同,电阻率大的功耗大,t值也较高。从(1)式和(2)式可以看出,要消除应力的影响,理想地应该有ΔLC=ΔLe,即:αC(tC-t0)=αe(te-t0)成立。在PTC陶瓷元件受电流冲击瞬时升温后,αC、tC的变化不大,而αe、te的大小却由电极的结构决定,因此如前所述,只能考虑调整电极成分来控制应力,其中影响最大的则是磷含量。磷含量越高,镀层的膨胀系数越小,电阻率也越高〔5〕。这样我们就不难发现,当磷含量较高时,因镀层电阻率高,冲击时功耗相对要大,温升te也随之增大,ΔLe就大。若ΔLe>ΔLC时,则产生压应力,当应力大到一定限度时,PTC元件发生层裂;反之当磷含量较低时,因镀层电阻率低,冲击时功耗相对要小,温升te也随之减小,ΔLe就变小。若ΔLe<ΔLC时,则产生张应力,当应力大到一定限度时,PTC元件发生碎裂。应力类型与磷含量的经验关系如图2所示。此外,应力大小和类型还受镀液的使用周期和镀层厚度〔6〕等因素的影响,它们关系比较复杂,尚待进一步探讨。
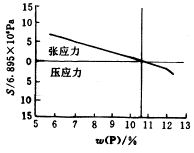
图2 镀层磷含量与应力的经验关系
3 结论
化学镀镍电极对PTC元件的耐工频电流冲击性能有很大的影响,这和化学镀镍镀层的应力有关。化学镀层中磷含量越高,镀层的压应力越大,PTC元件越易产生层裂。相反,化学镀层中磷含量越低,镀层的张应力越大, PTC元件越易产生碎裂。适当调整化学镀层中磷含量可得到耐工频电流冲击性能优良的PTC元件。